Table of Content
When there’s continuous contraction and expansion, the wire connections would loosen and cause the wire to creep out under the screws causing circuits to arc. As a result, aluminum wiring would routinely trip breakers, or worse, cause house fires. Many electrical devices used in the 1960s had smaller plain steel terminal screws, which made the attachment of the aluminum wires being used at that time to these devices much more vulnerable to problems. In the late 1960s, a device specification known as CU/AL (meaning copper-aluminum) was created that specified standards for devices intended for use with aluminum wire. Some of these devices used larger undercut screw terminals to more securely hold the wire. It is the aluminum wiring connections, rather than the wire itself, which are the real danger.
For that, there is the Copalum® system, from AMP Industries, the AlumiConn® Connector by King Innovations, the Purple Ideal 65® wire nut connector and “Kearny” split-bolt connectors. Unfortunately, pig-tailing repair methods are not a cure-all. The repeated bending strain imposed on the conductors during the retrofit process can damage the wire inside its insulation.
FREE PROGRAM TOUR
However, since the oxide layer is only a few nanometers thick, the added resistance is not noticeable under most conditions. When aluminum wire is terminated properly, the mechanical connection breaks the thin, brittle layer of oxide to form an excellent electrical connection. Unless this connection is loosened, there is no way for oxygen to penetrate the connection point to form further oxide. Light bulbs that burn out too fast could be the result of poor electrical connections. The outlet may draw an irregular flow of electricity from aluminum wiring, shorting out the bulb.
As a home inspector, it’s important to be able to provide your clients with accurate information to help with their big decisions. The best place to start is qualityhome inspector training, where inspectors can start learning or brush up on the truths behind common home systems, such as the electrical system. Let’s take a look at the real story behind aluminum wiring.
The True Story Behind Aluminum Wiring – Part One
Contractors used aluminum wiring because it was cheaper, flexible, and lightweight compared to copper. Aluminum has several properties that make it inferior to copper for wiring. Aluminum is a softer metal than copper, and besides being prone to damage during installation, it also expands more when heated.
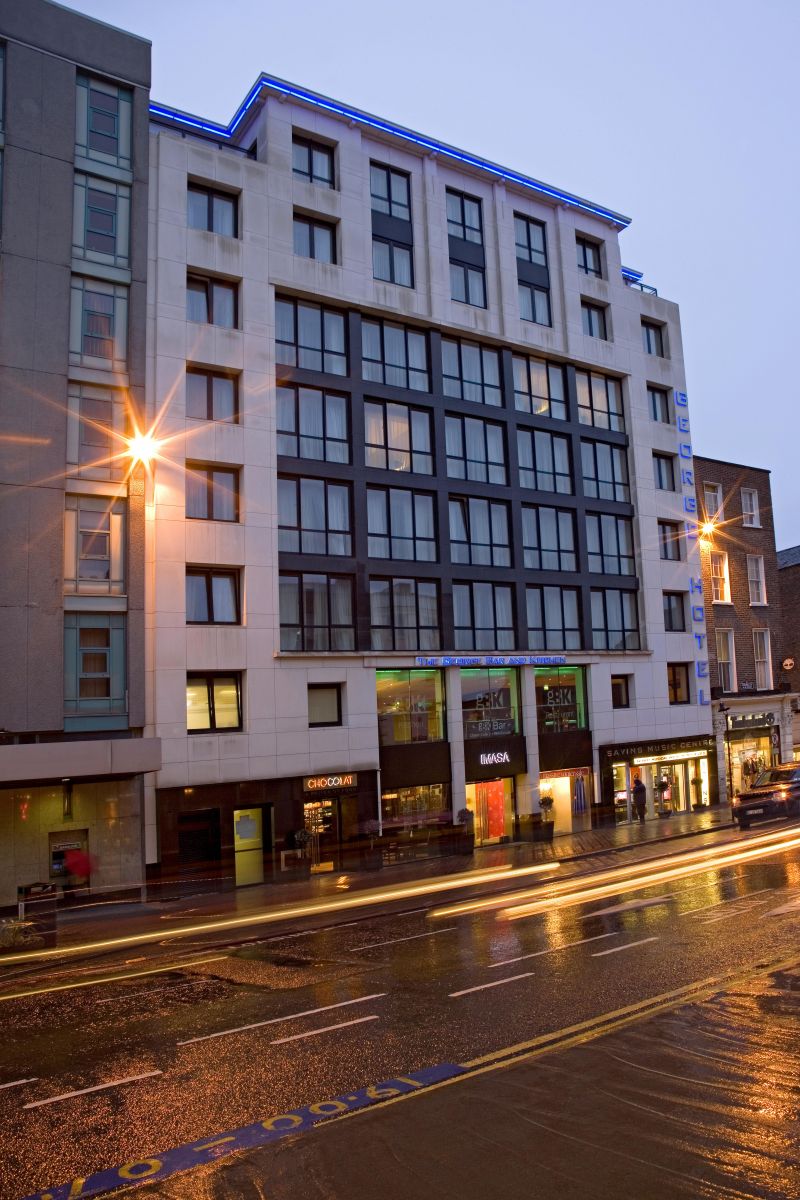
I am happy to see the government and insurance companies attempting to make homeowners aware of the dangers of having aluminum wiring. If you plan to buy a home with aluminum wiring, you may solve the problem through the methods we’ve discussed. Aluminum’s primary concern is not the wires themselves but the connections at outlets and switches. Aluminum got several problems after widespread adoption. Overheating was one of the significant issues that riddled aluminum wiring. Other issues include warm cover plates on receptacles and switches and flickering lights.
Branch Circuit Aluminum Wiring
One of the first signs your home may have aluminum wiring is that its electrical features fail to perform as well as they should. You may notice your lights flickering, or feel a warmth coming from your light switch cover plates. You might also observe scorch marks on the insulation covering your electrical wires or on the backs of your outlets if you remove them. If you are selling a home with aluminum wiring, it would be in your best interest to go ahead and have any potential repairs made prior to putting the home on the market. This way potential buyers will know the repairs have been made. If you supply them with a certification from a licensed electrician, you will make the process of obtaining home insurance easier for them.
The first step you should take in ensuring the safety of your home’s wiring is to have a licensed electrician perform an electrical inspection. Once you know the state of your wiring you can determine whether you need the implementation of safety measures or a complete rewiring. This is a question that is often asked and that has some misinformation regarding its answer. Aluminum Wiring is mostly safe, although there are some special considerations to be made when dealing with aluminum wiring. For the most part, homeowners have no problems with aluminum wiring, but when incorrect receptacles or conductors are installed, the threat of a hazard is likely. This resulted in a higher resistance junction, leading to additional overheating.
Unfortunately, there has been no research into the performance of the old and new solid aluminum wire alloys with both steel and brass connections to determine what impact the terminals had on connection performance. The National Electrical Code® has recognized conductors made of aluminum since for many years. Aluminum wiring was UL listed for residential use in 1946. The use of aluminum wire for feeders and service entrances was common by the early 1950’s and continues today. In the early 1960’s, Kaiser Aluminum and other aluminum manufacturers introduced solid-wire aluminum non-metallic sheathed cable. This wire was installed in the same manner as copper conductors, often with disastrous results.
The only problem was that they discovered the answers when too late. I got the same problem with our kitchen outlet and my mom has no idea as well of what to do. And when it comes to situations like this; it’s never a problem until it becomes one. Electrical panels and breakers marked AL-CU or CU-AL were also available. You might have difficulty getting home insurance, or you could be charged a higher premium. Aluminum deteriorates readily due to oxidation and galvanic corrosion (contact with moisture + certain metals).
Aluminum is one of the most versatile metals in existence, its use in the construction and electronics industry is infinite, however, it does not mean that it will always work at 100 percent. Some of the most common wiring damages have to do with aluminum wiring in homes. In the 1960’s and 70’s, aluminum wiring was used as a cheaper alternative to copper wire. That fact might have gotten you wondering if it’s cheaper, why isn’t it still used? The main problem with aluminum wiring is that it expands when it gets hot and then shrinks again when it cools off.
Aluminum alloys used for electrical conductors are only approximately 61% as conductive as copper of the same cross-section, but aluminum's density is 30.5% that of copper. Accordingly, one pound of aluminum has the same current carrying capacity as two pounds of copper. Since copper costs about three times as much as aluminum by weight (roughly US$3/lb vs. USD $1/lb as of 2017), aluminum wires are one-sixth the cost of copper wire of the same conductivity.
The examples and perspective in this article deal primarily with the United States and do not represent a worldwide view of the subject.
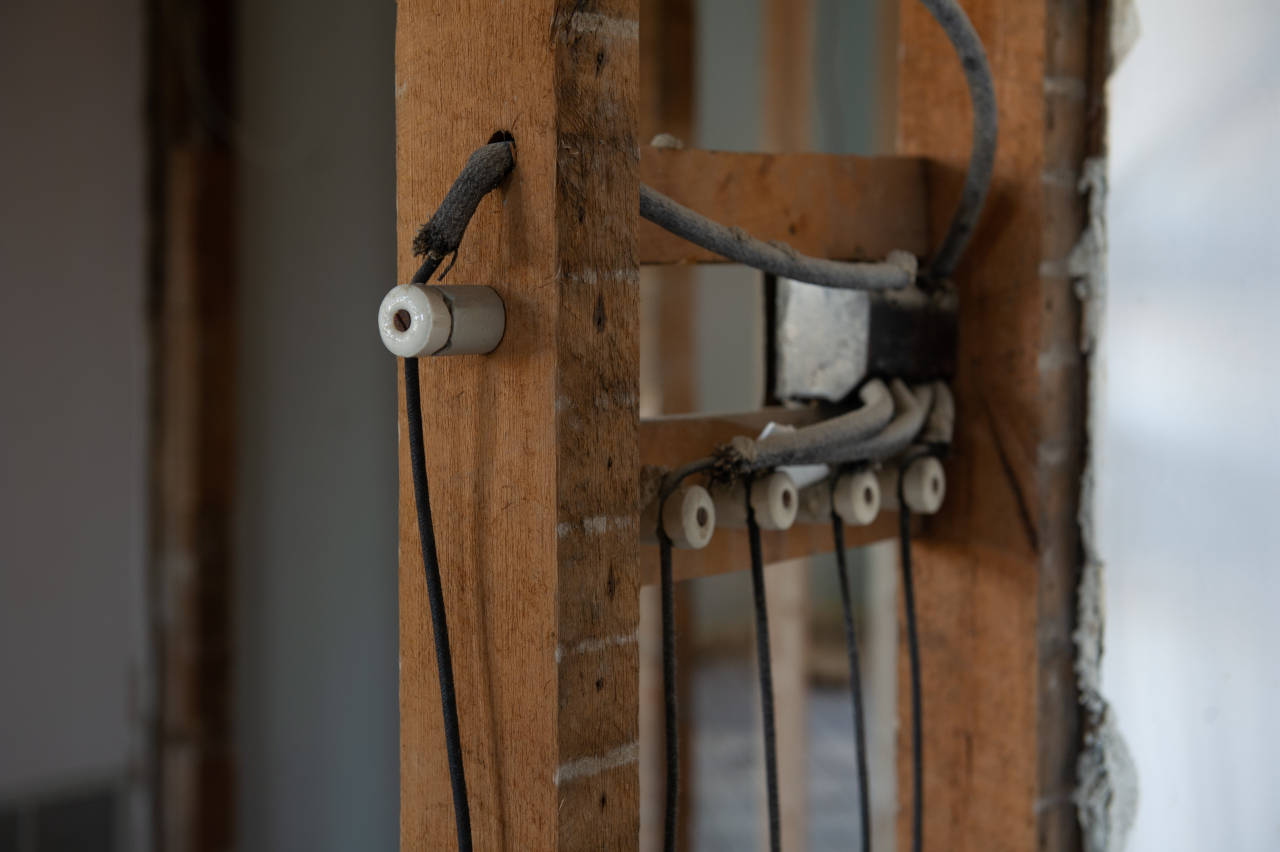
The Consumer Product Safety Commission warns that electrical connections in a house wired with pre-1972 aluminum wire is “55 times more likely … to reach Fire Hazard Conditions” than with copper. Stranded aluminum wires need a special joint compound that is electrically conductive and prevents rust. The stranded conductors are used on larger cables , typically used for large appliances like stoves and ovens. It is agreed that joint compound is a good practice on all aluminum wiring, but the compound is generally not required on solid conductors. Once you’ve added connectors or replaced the aluminum wires with copper, your home’s wiring will have increased durability, conductivity and protection from overheating.
Should I Have Sun Electrical Replace My Aluminum Wiring?
The expansion and contraction of the wire can lead to wire creeping out from its place under the screw holding it in place, causing loose wires and overheating. Another difference between aluminum and copper is oxidation. The layer that forms on copper conducts electricity easily, but aluminum oxide is a bad conductor of electricity, which can lead to overheating. COPALUM connectors use a special crimping system that creates a cold weld between the copper and aluminum wire, and is considered a permanent, maintenance-free repair.
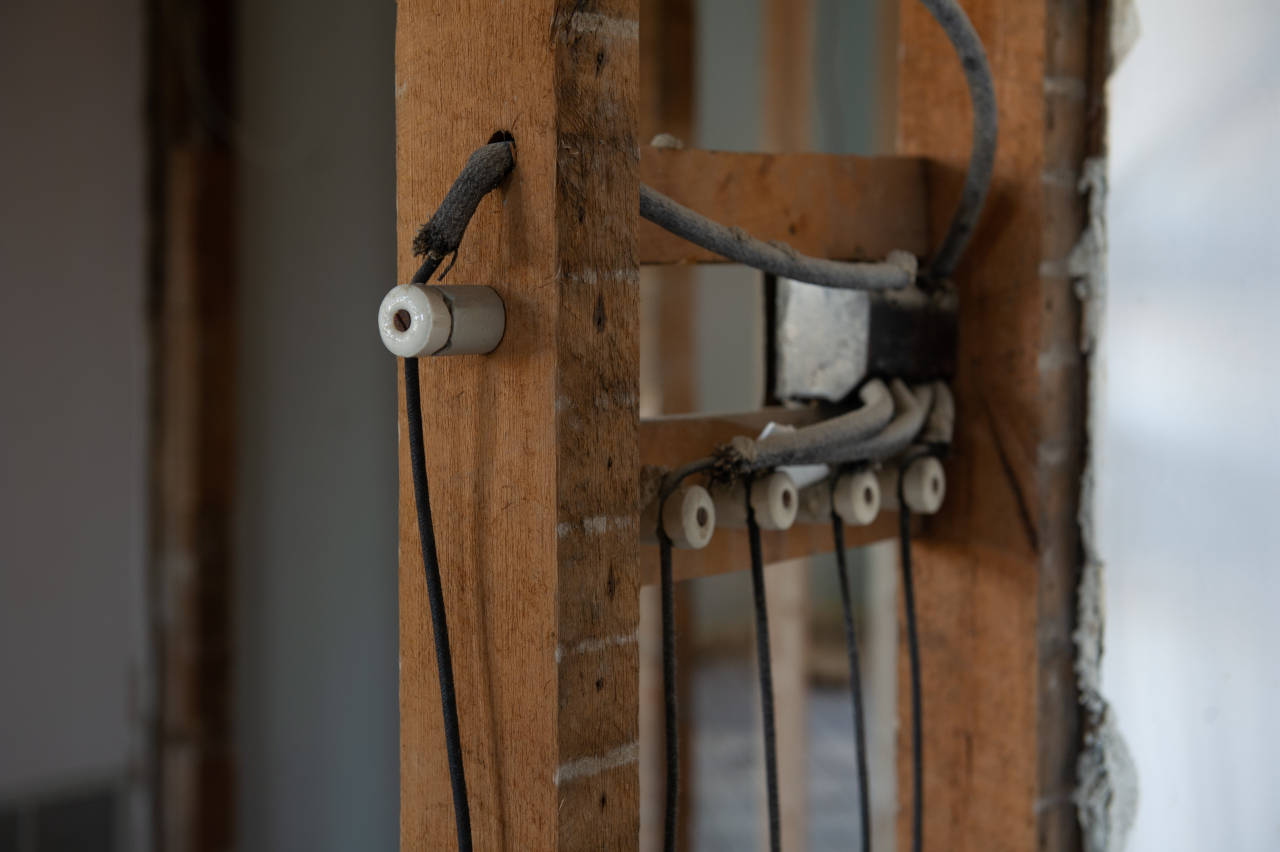